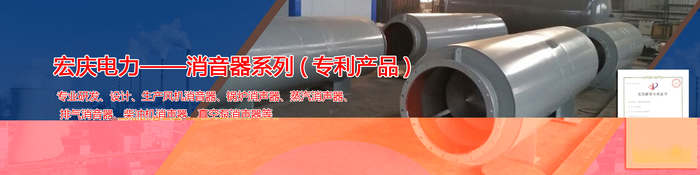
旋膜除氧器在水泥廠余熱電站中的實際應用情況分析?
在水泥廠余熱電站系統中,溶于鍋爐給水中的氧氣在高溫、高壓下很容易與設備及管道發生反應,使鍋爐各蒸發面、過熱面、汽水管道及汽輪機的運行安全和壽命受到威脅。同時,水中含有氣體,將增大傳熱熱阻,影響傳熱效率,降低系統的經濟性。因此除去鍋爐給水中的氧,對保證系統的安全、經濟運行事關重要。
水泥廠余熱電站常用除氧器及存在的問題
常用除氧器及其除氧原理
目前,水泥廠余熱電站中常用的除氧器有化學除氧器和低壓旋膜除氧器兩種。其他如真空除氧,解吸除氧、鐵屑除氧等水泥廠余熱電站不常用。
化學除氧器
江西水泥廠低溫余熱電站就采用了這種除氧器。其除氧原理是通過往鍋爐給水中加入藥劑,與氧氣發生反應從而達到除氧目的。余熱電站幾乎全部采用了這種除氧方式。其除氧原理滿足道爾定律———混合氣體的全壓等于各組成氣體分壓之和。對于化學除氧系統,由于往汽水系統內添加藥劑2尤其填中亞硫酸鈉3,使得鍋爐爐水含鹽量增加,這時需增加鍋爐的排污量來排走這些鹽分,因此增加了系統的汽水損失及熱量損失,增加了化學水制水量及處理化學水的藥品量等。
對于低壓旋膜除氧器,由于水泥窯況波動、電站負荷變化及低壓旋膜除氧器自身結構制約,使得水泥廠余熱電站的除氧系統運行效果不理想,存在許多問題。其主要問題有:
(除氧器不能穩定運行。水泥窯跑料、生產不穩定甚至停窯,使電站頻繁波動,引起旋膜除氧器工況波動頻繁,影響除氧效果。鍋爐給水溫度低。除氧器相當于一級回熱加熱器,對于低壓除氧器(大氣壓力式,其飽和水溫應為但在實際運行中,鍋爐給水溫度在-之間波動。鍋爐給水含氧量不合格,含氧量在7之間波動。
上述問題的存在首先與水泥廠整體運行水平有很大的關系。如果水泥窯運行平穩,則余熱電站工況相對穩定,水泥窯況的波動給除氧系統帶來的沖擊也會小一些,其次與以下問題有關。
第一,低壓旋膜式除氧器對電站熱力系統的波動適應能力弱。變工況下除氧器內壓力、溫度變化不一致會導致除氧惡化。如當進汽壓力升高時,溫度升高滯后于壓力,從而破壞了除氧器內氣與水的溶解平衡關系,使除氧器內水面上的氧氣由于壓力上升而又溶進水中,破壞除氧效果。另外低壓旋膜式除氧器因其傳熱傳質方式限制,其傳熱系數小,這也是其適應負荷波動能力弱的原因。
第二,汽機凝結水過冷卻增加了汽水中的溶氧量。如,對于帶補燃的余熱利用電站,往往不投汽輪機的三段抽汽,即不投低壓加熱器,而直接把凝結水打至疏水箱,然后用疏水泵打至余熱鍋爐,余熱鍋爐產生的熱水及飽和蒸汽再回至除氧器除氧。在把水打開至余熱鍋爐的過程中由于管路長,汽輪機凝結水由飽和水變成了欠飽和水。即過冷水,溫度降低,水中溶氧量增加,造成除氧不合格。
第三,由于在電站熱力系統內增加了余熱利用部分,因此在系統構成中較常規電站不可避免地增加了設備及泄露點,因此增加了系統內的溶氧量,這是無法克服的。我們只能通過各種方法減少系統不嚴密點及設法除去溶進的氧氣。
旋膜式除氧器結構特點及除氧原理
旋膜式除氧器的除氧原理與低壓旋膜式除氧器相同,均屬熱力除氧。但其結構形式與低壓旋膜式除氧器不同。旋膜式除氧器采用旋流式起膜管,汽機凝結水從射流孔切向進入旋流管內形成中空的、高速旋轉的水膜裙與被加熱蒸汽進行熱量、質量交換。旋流管中的熱交換主要有兩個過程:一是加熱蒸汽的凝結換熱過程,包括蒸汽與水的對流換熱和蒸汽在水膜表面的凝結換熱;二是射流的卷吸過程,當凝結水從射流孔射入后,在旋膜管內形成高速旋轉水膜,由于水膜的高速旋轉,在靠近水膜處形成低壓區,使得大量蒸汽被卷吸入水膜內,從而使凝結水迅速被加熱。其中起膜管是其關鍵部件8#9。除氧器的除氧過程不僅是一個傳熱過程,也是一個傳質過程。因此在除氧時必須建立良好的傳熱條件,即要有足夠的熱量及較高的傳熱系數,把水迅速加熱到飽和溫度。同時須建立較好的氣體自水中離析的傳質條件,即保證足夠的汽(氣,水接觸面積和不平衡壓差。
旋膜式除氧器不同于其它除氧器的關鍵之處在于其噴淋結構造成的汽水傳熱傳質方式不同。旋膜式除氧器入口水采用起膜管裝置噴淋,汽機凝結水在起膜管中形成射流噴濺及旋膜,并在起膜管出口形成水膜裙,其傳熱系數遠比其他類型熱力除氧器高。其優點如下:
1、除氧效果好。保證鍋爐給水含溶氧量適應性強。2、能滿足水泥窯的工況波動。3、穩定性好當負荷突變、瞬間補給水量突變、改用不同參數汽源及入口水溫突降時,除氧水質仍能保持合格,并可在的額定負荷下長期穩定運行。4、節能節水。排汽量小于入口水量,減少汽水損失及熱量損失。